To resume many of the lean principles of a company or attitude, one book is key. From the must-read book The Toyota Way: 14 Management Principles from the World’s Greatest Manufacturer (Dr Jeffrey Liker), Wikipedia, and other sources, with our own comments and additions, read on.
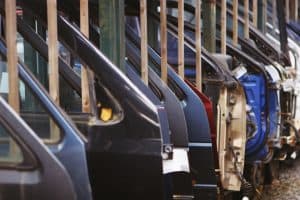
Toyota is among, if not the top, initial Lean practitioners at a big scale. The automotive industry asking for high volumes, high quality, and safety, yet with reasonable prices taking the complexity, materials, studies, and labor needed into account.
(FYI, the book/Wikipedia terminology is used for the lean principles to ease communication)
The 14 Lean Principles
Category | Toyota Lean Principles ©J. Liker | Our Comments | |
Long-term philosophy | 1 | Base your management decisions on a long-term philosophy, even at the expense of short-term financial goals | Obliges to define a long-term objective, and planning for these, including a budget, HR … Refer to the Hoshin Kanri methodology to help here |
The right process will produce the right results | 2 | Create a continuous process flow to bring problems to the surface | Not only process but company attitude. It involves at minimum manufacturing + HR + Quality + Customer Support No finger-pointing. Should be seen as an opportunity as in Golden Nuggets for innovation. |
3 | Use “pull” systems to avoid overproduction | Look at the ERP, its settings may help or not here … Note: this is the tip of the iceberg KPI. No process will be capable of Just In Time if too much WIP, or random Quality … Structure your process in autonomous sub-teams, with some defined and controlled decision-making and problem-solving power. | |
4 | Level out the workload (heijunka). (“Work like the tortoise, not the hare“). | Key for production organization: start with Takt Time definition and then level the individual processes cycle times to avoid bottlenecks or over-capacities. More on that in all process posts. | |
5 | Build a culture of stopping to fix problems, to get quality right the first time | Among others, see Design for Six Sigma (DfSS) articles | |
6 | Standardized tasks and processes are the foundation for continuous improvement and employee empowerment | No process can be measured and therefore improved if not repeatable. Standardization is the first step before drawing any conclusion Real case: during an audit at a supplier’s assembly line, while observing that there was no instruction available for the workers at all, the answer was “Operators have all instructions in their head” :( | |
7 | Use visual control so no problems are hidden | ||
8 | Use only reliable, thoroughly tested technology that serves your people and processes | Is part of the technology selection. Needs to involve the full team (quality, process, purchasing) even -or especially- at the R&D phase. Reminder, 80% of the cost is decided at the design phase … so as later Quality KPIs. See Agility and modern times about that. | |
Add value to the organization by developing your people
| 9 | Grow leaders who thoroughly understand the work, live the philosophy, and teach it to others. | very structure-dependent (not all companies are Toyota). Long-term leaders are ideal of course, but less and less the case in smaller Agile organizations (refer below). Other means of building and keeping know-how are also needed. |
10 | Develop exceptional people and teams who follow your company’s philosophy | ||
11 | Respect your extended network of partners and suppliers by challenging them and helping them improve | not only formal audits but even more upstream workshops, on-site continuous improvement, Kaizen, Blitz … Tip: have your own clients participate in your activities, so as you with your suppliers | |
Continuously solving root problems drives organizational learning
| 12 | Go and see for yourself to thoroughly understand the situation (Genchi Genbutsu) | ≈ “where the value is created” philosophy. Not only for HR efficiency but one of the keys to helping design the next product with production technologies and means in mind |
13 | Make decisions slowly by consensus, thoroughly considering all options; implement decisions rapidly (nemawashi) | again, less and less the case in smaller Agile organizations (refer below) | |
14 | Become a learning organization through relentless reflection (hansei) and continuous improvement (kaizen) | Do put a process in place to formally capitalize the know-how. This is more and more needed as developers and teams are moving. Tip: do separate the know-how from the mandatory company procedures (not to have to learn and validate 200+ procedures before starting to work when you join a company … all but Agile organization) |
Lean Principles vs Agile Organisation
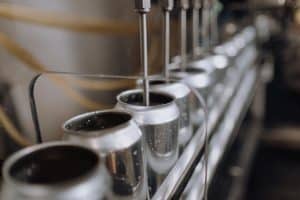
There is one aspect where these 14 Lean Principles are a bit outdated or would need some update: the Agility aspect of some models of modern organizations and development:
- technologies and rhythm of changes evolve exponentially
- customer demands, competition, and suppliers evolve very rapidly. Not on time = zero sell
- people change much more jobs and the company
- remote companies, remote work, and more and more outsourced teams and functions
So the lean principles #8, #9, #10, #13 would need to be amended, so as in some aspects #5
In some markets, having a new product every 1-2 years is a must
…whether we like it or not (especially for the ecological aspect).
Ex: producing a new reliable high-volume phone model every year, implies either having technologies being chosen and validated years ahead or having an extremely efficient R&D, V&V, and production process. Most of the time both … or prepare your Customer Support team and financials to face issues or market recalls (antenna less effective, battery catching fire, foldable screens cracking …)
A Technology Roadmap process implemented in your R&D department is a must for this.
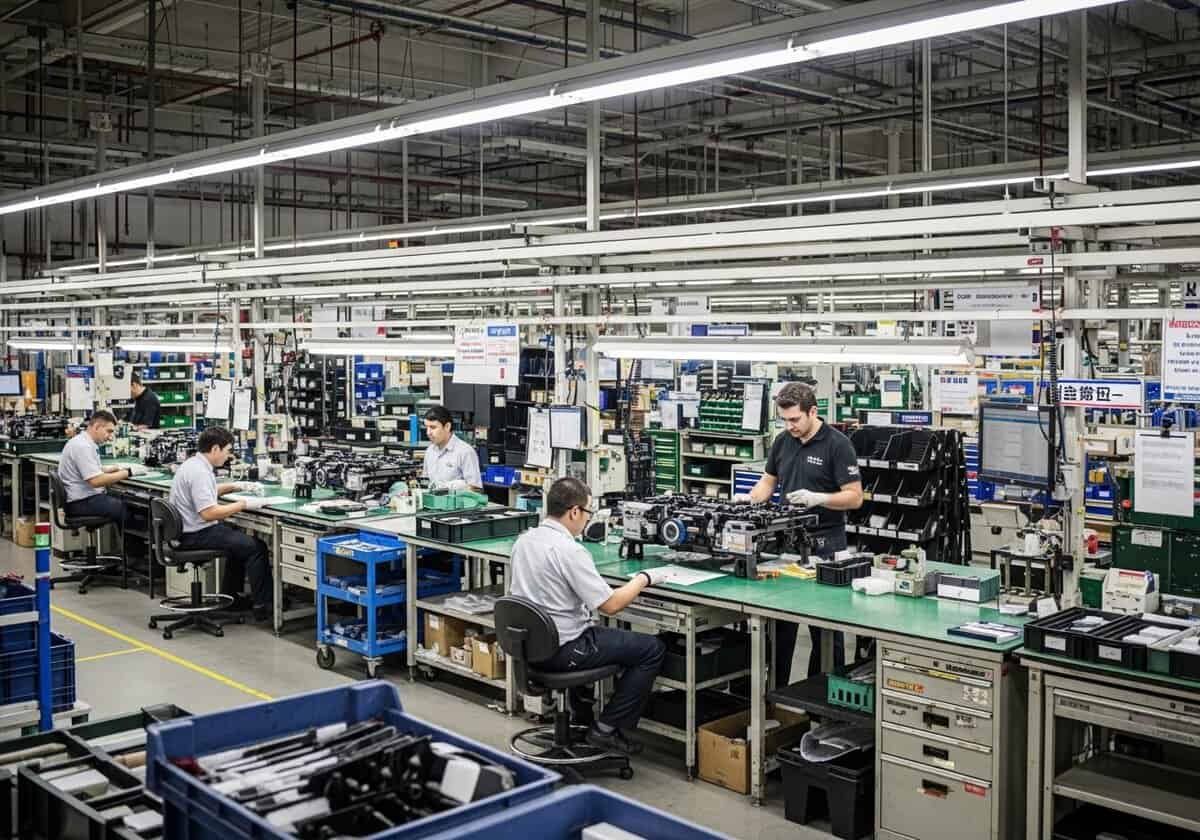
Complementary Readings and Related Methods
- Value Stream Mapping: a visual tool to analyze and design the flow of materials and information required to bring a product to the customer.
- Kaizen (Continuous Improvement): a philosophy that focuses on continuous, incremental improvement in processes, products, and services.
- 5S Methodology: a workplace organization method that uses a list of five Japanese words (Seiri, Seiton, Seiso, Seiketsu, Shitsuke) to create an efficient and effective workspace.
- Just-In-Time (JIT) Production: a strategy that aligns raw-material orders from suppliers directly with production schedules to reduce inventory costs.
- Root Cause Analysis (RCA): a method for identifying the underlying causes of problems to prevent recurrence and improve processes.
- Design for Manufacturability (DFM): an engineering practice that focuses on designing products so they are easy to manufacture, reducing costs and time.
- Failure Mode and Effects Analysis (FMEA): a systematic method for evaluating processes to identify where and how they might fail and assessing the relative impact of different failures.
- Total Productive Maintenance (TPM): an approach that aims to increase productivity by reducing downtime and improving equipment reliability.
- Agile Methodology: a project management and product development approach that emphasizes flexibility, collaboration, and customer feedback.
- Six Sigma: a data-driven approach and methodology for eliminating defects in any process, aiming for near perfection in quality.
- Concurrent Engineering: a method that emphasizes the parallelization of tasks (such as design and manufacturing) to improve product development time and efficiency.
- Sustainable Design and Manufacturing: practices that prioritize environmental responsibility and resource efficiency in product design and production processes.
I agree that separating know-how from mandatory procedures can enhance onboarding and flexibility, especially as remote work and frequent job changes become the norm.
Implementing a Technology Roadmap in R&D can indeed help companies stay ahead by ensuring efficient development processes while minimizing the risk of costly product recalls.
It would be interesting to see how these principles adapt to smaller, more agile companies that may not have the resources or structure of a giant like Toyota.
Interesting article! But does anyone else feel that Agile organizations might actually benefit more from these 14 lean principles?
Interesting read! But arent Lean Principles more suitable for manufacturing sectors rather than service industries? Thoughts?
Interesting read! Ever wonder if these 14 Lean Principles could be effectively applied to non-manufacturing sectors like education or healthcare?
Related Posts
Product Value Analysis Overview
Workstation Ergonomic Assessment
Engineering Change Order (ECO): Best Practices to Minimize Disruption and Cost
From Lab To Market: The Role of the Pilot Production Run
45+ More Cognitive Science Tricks for Games and Marketing: Psychological and Engagement
45+ Cognitive Science Tricks for Games and Marketing: Psychological and Engagement