For Manufacturing: the Japanese Lean terms are must-know vocabulary in manufacturing or quality as these have no direct equivalent and are used as-is in an industrial context.
There are a variety of Japanese manufacturing lean terms, but we list here a shortlist of Japanese terms to know in Lean Sigma, and more generally in any plant, product, or process improvement. Not for a show-off attitude, but because these are usually more concise and dedicated than their translation equivalent; and simply because there ARE commonly used lean terms in western industries by now.
Japanese Lean Terms
Kaizen
A key vocabulary to start the Lean terms list is Kaizen meaning literally
Kaizen “Change for the good” = improvement
or “change for the better”. All Lean activities are aimed at this continuous Kaizen. It emphasizes continuous improvement in all areas of business. Kaizen is based on the idea that small, incremental changes can lead to big results over time. The goal of kaizen is to eliminate waste and improve efficiency in all aspects of the manufacturing process.
Kaizen is a team-based approach that relies on the collective input of workers to identify and implement improvements. This bottom-up approach to problem-solving ensures that everyone in the organization has a vested interest in the success of the company and that improvements are based on the real needs of those who are doing the work. This approach helps to ensure that waste is constantly being removed from the manufacturing process. The Lean manufacturing production methodology focuses on minimizing waste in all forms, including overproduction, defects, inventory, motion, and waiting time as seen in Mudas hereafter.
Kaizen is a key component of Lean manufacturing, as it provides a mechanism for continual improvement that can be quickly implemented and adapted as new problems and opportunities arise as seen below with the other lean terms.
Kanban
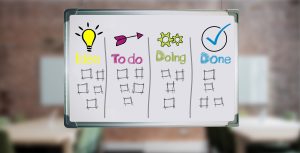
Kanban, with its Japanese word meaning “sign“ or “billboard”, is a tool that helps to visualize the process, its current state, and its targets, and more generally to schedule and optimize the flow of work in a lean and just–in–time (JIT) manufacturing.
A kanban usually takes the form of very visual boards where the work in process is represented by cards that are moved along the line as the work progresses, such as:
-
- Kanban boards to track work in progress and visualize the flow of work. This can help identify bottlenecks and areas for improvement when cards get stuck and/or empty slots appear
- Kanban sheets to manage inventory levels. This can help ensure that materials are available when needed, in a pull organization, and help reduce waste.
- Kanban to schedule production to help ensure that work is flowing smoothly and that deadlines are met
- Kanban boards to track quality by identifying issues early and ensuring that products meet customer expectations
Tip: as with project scorecards, or sprint or scrum boards, be very visual: use a mix of simple shapes (square, circles, triangle) and easy color coding to convey the message.
Tip: it must be located close to the worker (in the Gemba, see below) and have sufficient free space nearby to permit very quick daily team meetings in front of it
Anyone just passing by, even unfamiliar with the process, must see the state and the ongoing challenge in the blink of an eye
Gemba
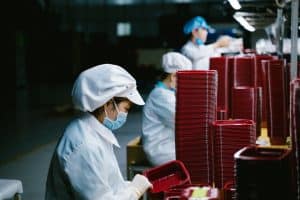
Gemba is a Japanese Lean term that means “the real place.” In lean manufacturing, Gemba is the place where the value is added to the product. This could be the factory floor, the office for a service, or any other place where useful work for the customer is performed.
The goal of lean is to eliminate waste in all forms, and Gemba is where waste is most likely to occur. By identifying and eliminating waste at the source, lean manufacturing strives to create a more efficient and effective workplace.
Muda
From 無駄 = “Useless”, by extension waste or unnecessary work. In Lean manufacturing, muda is used to refer to waste that occurs when workers are performing
any tasks that do not add value to the product or service
This can include things like waiting for materials, waiting for approvals, or performing tasks that could be automated. Eliminating muda(s) will help to improve efficiency and reduce costs in manufacturing and other types of businesses. The Lean methodology has identified 7 family types of Mudas, the 7 wastes of Lean:
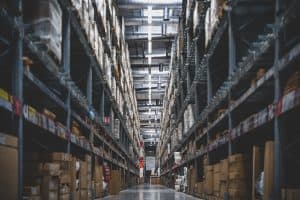
-
- Transport
- Inventory
- Motion
- Waiting
- Over-Processing
- Overproduction
- Defects
which can easily be remembered by “TIMWOOD” (first letter of each waste)
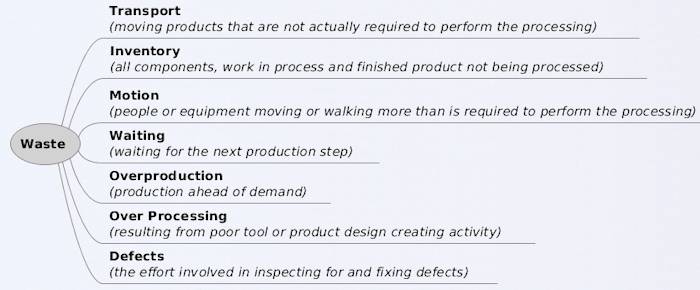
Bonus: it is sometimes mentioned an 8th Muda: waste of talent: the fact of not utilizing available HR talent efficiently
Poka-Yoke
Poka–yoke is a Japanese quality control term derived from the Japanese words “poka” which means avoid, and “yokeru” which means a mistake. It is a physical technique for preventing mistakes or errors in a process, by making them either literally impossible or at least highly improbable
- a tool with a keyed pattern that can not enter into another hole
- a shelf that can only hold a specific dedicated part or only one part
Poka–yoke devices or methods are used to make a process easier to understand and follow to prevent errors without any later effort by becoming idiot-proof.
Poka-yoke can be used in various manufacturing processes to improve quality control.
Examples of Poka-Yoke:
-
- a door that opens in the direction that a person is facing. This ensures that the person is not trying to enter the room the wrongway, making the walk...
You have read 65% of the article. The rest is for our community. Already a member? Log in
(and also to protect our original content from scraping bots)
Innovation.world community
Login or Register (100% free)
View the rest of this article and all members-only content and tools.
Only real engineers, manufacturers, designers, marketers professionals.
No bot, no hater, no spammer.
Isnt the concept of Gemba just common sense in any industry? Why is it hailed as uniquely Japanese?
Poka-yoke is an incredibly effective approach for enhancing quality control by preemptively addressing potential errors.
As someone involved in manufacturing, I’ve seen firsthand how adopting these methodologies not only optimizes workflow but also empowers employees to actively contribute to the success and innovation of the organization.
This article provides a great introduction to key lean manufacturing concepts like Heijunka and Andon, which are crucial for optimizing production efficiency and quality control. Implementing these strategies can significantly enhance responsiveness to customer demands and reduce waste in manufacturing processes.
Interesting read! But isnt Jidoka also a key lean term? Why wasnt this included in your list of Japanese Lean Terms?
Related Posts
Product Value Analysis Overview
Workstation Ergonomic Assessment
Engineering Change Order (ECO): Best Practices to Minimize Disruption and Cost
From Lab To Market: The Role of the Pilot Production Run
45+ More Cognitive Science Tricks for Games and Marketing: Psychological and Engagement
45+ Cognitive Science Tricks for Games and Marketing: Psychological and Engagement