Per riprendere molti dei principi lean di un'azienda o di un atteggiamento, un libro è fondamentale. Dal libro imperdibile Il Toyota Way: 14 principi di gestione dal più grande produttore del mondo (Dr. Jeffrey Liker), Wikipedia e altre fonti, con i nostri commenti e le nostre aggiunte, continuate a leggere.
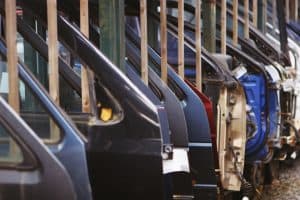
Toyota è tra i primi, se non il primo, praticanti di Lean su larga scala. L'industria automobilistica chiede volumi elevati, alta qualità e sicurezza, ma a prezzi ragionevoli, tenendo conto della complessità, dei materiali, degli studi e della manodopera necessari.
(Per vostra informazione, il libro/Wikipedia per i principi lean viene utilizzata una terminologia che facilita la comunicazione)
I 14 principi Lean
Categoria | Principi Toyota Lean ©J. Liker | I nostri commenti | |
Filosofia a lungo termine | 1 | Basate le vostre decisioni di gestione su una filosofia a lungo termine, anche a scapito degli obiettivi finanziari a breve termine. | Obblighi di definire un obiettivo a lungo termine, e la pianificazione per questi, tra cui un budget, HR ... Per aiutarvi, fate riferimento alla metodologia Hoshin Kanri. |
Il giusto processo produrrà i giusti risultati | 2 | Creare un flusso continuo di processi per far emergere i problemi. | Non solo processo, ma anche atteggiamento aziendale. Coinvolge almeno la produzione + le risorse umane + la qualità + l'assistenza ai clienti. Non bisogna puntare il dito. Dovrebbe essere visto come un'opportunità, come in Pepite d'oro per l'innovazione. |
3 | Utilizzare sistemi "pull" per evitare la sovrapproduzione | Guardate l'ERP, le sue impostazioni possono essere utili o meno ... Nota: questa è la punta dell'iceberg KPI. Nessun processo sarà in grado di funzionare "Just In Time" se ci sono troppi WIP o una qualità casuale ... Strutturate il processo in sottogruppi autonomi, con un potere decisionale e di risoluzione dei problemi definito e controllato. | |
4 | Livellare il carico di lavoro (heijunka). (“Lavorare come la tartaruga, non come la lepre“). | Chiave per l'organizzazione della produzione: iniziare con la definizione del Takt Time e poi livellare i tempi di ciclo dei singoli processi per evitare colli di bottiglia o sovraccapacità. Maggiori informazioni in tutti i post sui processi. | |
5 | Costruire una cultura che prevede di fermarsi per risolvere i problemi, per ottenere la qualità giusta al primo tentativo. | Tra gli altri, si veda Progettazione per Sei Sigma (DfSS) articoli | |
6 | Attività e processi standardizzati sono alla base del miglioramento continuo e della responsabilizzazione dei dipendenti. | Nessun processo può essere misurato e quindi migliorato se non è ripetibile. La standardizzazione è il primo passo da compiere prima di trarre qualsiasi conclusione. Un caso reale: Durante un audit presso la linea di assemblaggio di un fornitore, osservando che non c'era alcuna istruzione disponibile per i lavoratori, la risposta è stata "OI peratori hanno tutte le istruzioni nella loro testa” :( | |
7 | Utilizzare il controllo visivo per non nascondere i problemi | ||
8 | Utilizzate solo tecnologie affidabili e accuratamente testate, al servizio delle vostre persone e dei vostri processi. | Fa parte della selezione della tecnologia. Deve coinvolgere l'intero team (qualità, processo, acquisti) anche - o soprattutto - nella fase R&D. Ricordiamo che l'80% del costo viene deciso nella fase di progettazione... così come i successivi KPI di qualità. Si veda Agilità e tempi moderni a questo proposito. | |
Aggiungete valore all'organizzazione sviluppando le vostre persone
| 9 | Crescere leader che comprendano a fondo il lavoro, vivano la filosofia e la insegnino agli altri. | molto dipendente dalla struttura (non tutte le aziende sono Toyota). I leader a lungo termine sono l'ideale, naturalmente, ma sempre meno nelle organizzazioni Agile più piccole (vedi sotto). Sono necessari anche altri mezzi per costruire e mantenere il know-how. |
10 | Sviluppare persone e team eccezionali che seguano la filosofia della vostra azienda. | ||
11 | Rispettare la propria rete estesa di partner e fornitori mettendoli alla prova e aiutandoli a migliorare | non solo audit formali, ma anche workshop più a monte, miglioramento continuo in loco, Kaizen, Blitz ... Mancia: far partecipare i vostri clienti alle vostre attività, così come voi con i vostri fornitori | |
La soluzione continua dei problemi alla radice favorisce l'apprendimento organizzativo
| 12 | Andare a vedere di persona per capire a fondo la situazione (Genchi Genbutsu) | ≈ La filosofia "dove si crea il valore". Non solo per l'efficienza delle risorse umane, ma anche per aiutare a progettare il prossimo prodotto tenendo conto delle tecnologie e dei mezzi di produzione. |
13 | Prendere decisioni lentamente, per consenso, valutando a fondo tutte le opzioni; attuare le decisioni rapidamente (nemawashi). | di nuovo, sempre meno nelle organizzazioni Agile più piccole (vedi sotto). | |
14 | Diventare un'organizzazione che apprende attraverso una riflessione incessante (hansei) e un miglioramento continuo (kaizen). | Mettete in atto un processo per capitalizzare formalmente il know-how. Questo è sempre più necessario, dato che gli sviluppatori e i team si stanno spostando. Mancia: separare il know-how dalle procedure aziendali obbligatorie (non dover imparare e convalidare 200+ procedure prima di iniziare a lavorare quando si entra in un'azienda ... tutto tranne l'organizzazione Agile) |
Principi Lean vs Organizzazione Agile
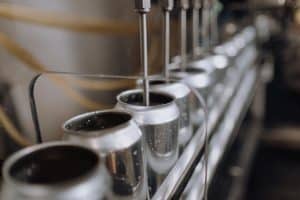
C'è un aspetto in cui questi 14 principi Lean sono un po' datati o avrebbero bisogno di qualche aggiornamento: il Aspetto dell'agilità di alcuni modelli di organizzazioni moderne e di sviluppo:
- le tecnologie e il ritmo dei cambiamenti si evolvono in modo esponenziale
- Le richieste dei clienti, la concorrenza e i fornitori si evolvono molto rapidamente. Non in tempo = zero vendite
- le persone cambiano molto più spesso lavoro e l'azienda
- aziende remote, lavoro a distanza e un numero sempre maggiore di team e funzioni esternalizzate
Pertanto, i principi lean #8, #9, #10, #13 dovrebbero essere modificati, in quanto in alcuni aspetti #5
In alcuni mercati, avere un nuovo prodotto ogni 1-2 anni è un must.
...che ci piaccia o no (soprattutto per l'aspetto ecologico).
Es: produrre un nuovo affidabile Ogni anno un modello di telefono ad alto volume implica la scelta e la validazione delle tecnologie con anni di anticipo oppure un processo di R&D, V&V e produzione estremamente efficiente. Nella maggior parte dei casi entrambi ... o preparate il vostro team di assistenza clienti e le vostre finanze ad affrontare problemi o ritiri dal mercato (antenna meno efficace, batteria che prende fuoco, schermi pieghevoli che si rompono ...).
A Tabella di marcia della tecnologia Il processo implementato nel vostro reparto R&D è un must per questo.
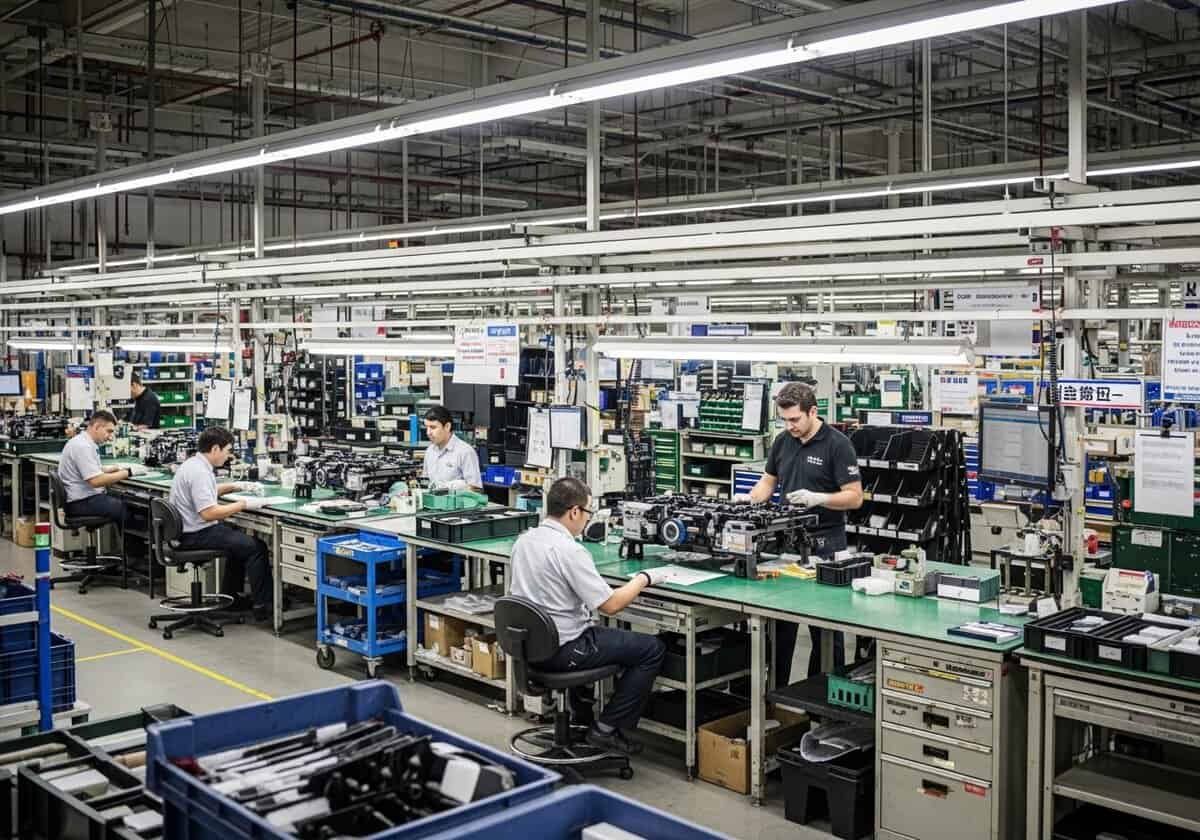
Letture complementari e metodi correlati
- Mappatura del flusso di valore: uno strumento visivo per analizzare e progettare il flusso di materiali e informazioni necessario per portare un prodotto al cliente.
- Kaizen (miglioramento continuo): una filosofia che si concentra sul miglioramento continuo e incrementale di processi, prodotti e servizi.
- 5S Metodologia: un metodo di organizzazione del posto di lavoro che utilizza un elenco di cinque parole giapponesi (Seiri, Seiton, Seiso, Seiketsu, Shitsuke) per creare uno spazio di lavoro efficiente ed efficace.
- Produzione Just-In-Time (JIT): una strategia che allinea gli ordini di materie prime dai fornitori direttamente con i programmi di produzione per ridurre i costi di inventario.
- Analisi delle cause (RCA): un metodo per identificare le cause alla base dei problemi per evitare che si ripetano e migliorare i processi.
- Progettazione per la producibilità (DFM): una pratica ingegneristica che si concentra sulla progettazione di prodotti facili da fabbricare, riducendo i costi e i tempi.
- Analisi delle modalità e degli effetti dei guasti (FMEA): un metodo sistematico di valutazione dei processi per identificare dove e come potrebbero fallire e per valutare l'impatto relativo dei diversi fallimenti.
- Manutenzione Produttiva Totale (TPM): un approccio che mira ad aumentare la produttività riducendo i tempi di fermo e migliorando l'affidabilità delle apparecchiature.
- Metodologia Agile: un approccio alla gestione dei progetti e allo sviluppo dei prodotti che enfatizza la flessibilità, la collaborazione e il feedback dei clienti.
- Six Sigma: un approccio e una metodologia basati sui dati per eliminare i difetti in qualsiasi processo, puntando a una qualità quasi perfetta.
- Ingegneria concorrente: un metodo che enfatizza la parallelizzazione dei compiti (come la progettazione e la produzione) per migliorare i tempi e l'efficienza dello sviluppo del prodotto.
- Progettazione e produzione sostenibile: pratiche che privilegiano la responsabilità ambientale e l'efficienza delle risorse nella progettazione dei prodotti e nei processi produttivi.
Sono d'accordo sul fatto che separare il know-how dalle procedure obbligatorie può migliorare l'onboarding e la flessibilità, soprattutto quando il lavoro a distanza e i frequenti cambiamenti di lavoro diventano la norma.
L'implementazione di una roadmap tecnologica in R&D può effettivamente aiutare le aziende a essere all'avanguardia, garantendo processi di sviluppo efficienti e riducendo al minimo il rischio di costosi richiami di prodotto.
Sarebbe interessante vedere come questi principi si adattino ad aziende più piccole e agili che potrebbero non avere le risorse o la struttura di un gigante come Toyota.
Articolo interessante! Ma c'è qualcun altro che ritiene che le organizzazioni Agile possano beneficiare maggiormente di questi 14 principi lean?
Una lettura interessante! Ma i principi Lean non sono più adatti al settore manifatturiero che a quello dei servizi? Opinioni?
Una lettura interessante! Vi siete mai chiesti se questi 14 principi Lean potrebbero essere applicati efficacemente a settori non manifatturieri come l'istruzione o la sanità?
Post correlati
I 20 Migliori Utilizzi dei Proxies per l'Ingegneria
Come Vendere Ghiaccio Agli Eschimesi (ovvero Trucchi di Marketing)
Greenwashing: i 15 migliori consigli di un gentiluomo per un inganno squisito
Come combattere al meglio un brevetto in sospeso
Tutti gli stati dei brevetti: PCT vs Brevetto in attesa vs Brevetto pubblicato vs Brevetto concesso
Le 10 migliori strategie e strumenti per l'invalidazione dei brevetti