Want to increase production & team efficiency in a lean way with SMED? Want to achieve the shortest cycle time (with a lot of human resources)? Follow the organization of F1 pros from the RedBull team:
SMED in Formula 1 Teams
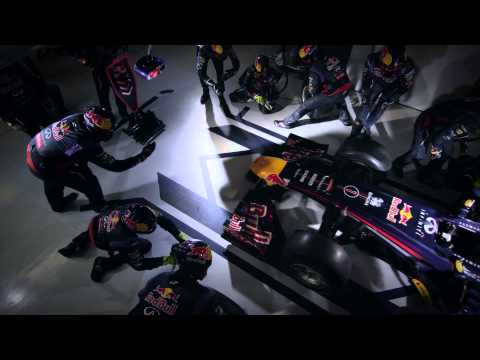
Just to tease them a bit: the two screwing tools lying on the floor at the beginning … maybe a bit of 5S ?
The refueling was missing in the video above, so some also really interesting details on the fueling part, with some look on the quick connector (is that a big Stäubli style connector, but huge?) + locking mechanism + the ergonomic of the 2 positions handle + security for 12L/seconds fuel flow.
Notice also on the communication system within the team with in-helmet status LED indicators (Google glass a decade before ?) + independent operator, for efficiency so as for security
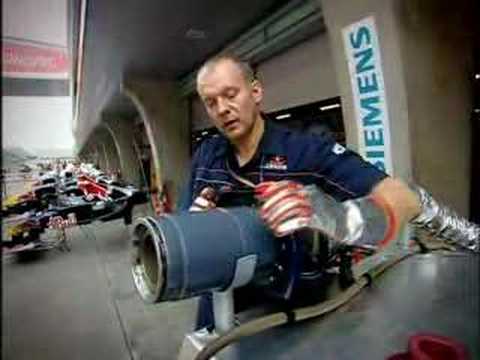
To be compared with the method in the 1950s and then with another great brand, Ferrari in 2013:
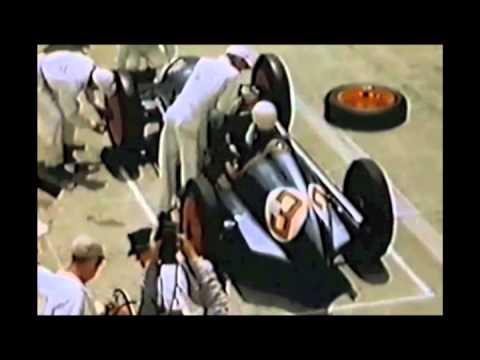
SMED in 1950
To take his own words, requiring “Just 67 seconds after the driver stopped”
We particularly appreciated the guy jumping, again and again, to lift the car with his weight & hammer work to tighten and untighten a hand-placed nut, clearly, the limiting factor of that process; dedicated tooling and design of wheel change connection (real usage condition when design!) is an important part of SMED. The regulation of max 4 crew members working on the pit stop surprisingly includes the driver -he just turns the wheels one-.
SMED by Ferrari in 2013
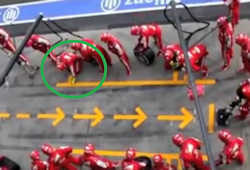
The top view permits to watch a 3-guys-per-wheel team well (look in detail and compared the work of four teams, one per wheel)
We particularly like the 3rd guy from the top left, removing a kind of small part or grit on the floor. At this high level, failure could come from any uncontrolled small detail.
But just to tease this team also, if that was an industrial application, calculate the productivity, knowing that we see at least 21 guys, with probably more off the screen … and compare to 1950 score.
Productivity=nb of units produced/person/unit of time
From the movies above, in industrial applications, the more general challenge could come from being efficient at reproducing that in series, the entire shift long, like in plant production (not throwing the wheel away for example, that works only if you have only a few to do and nothing around), but that would be a different situation.
be also sure about your Risk Analyse & FMEA of the guy in front of the car, waiting to lift the car, in case the car does not stop, or 1m too late…
(Do not rely on a human pushing the brake at the right millisecond, 100% of the time. In such case, in a plant situation, a mechanical stop built in the concrete, moving up or down could be an option, maybe lifting the car also at the same time?)
Complementary Readings & Methods
- 5S Methodology: Organizing the workplace to increase efficiency and reduce waste.
- Just-In-Time (JIT) Production: Producing only what is needed, when it is needed, which can be facilitated by quick changeovers.
- Poka-Yoke (Error Proofing): Implementing mechanisms to prevent errors, which can be critical during rapid changeovers.
- Standard Work: Developing standardized procedures to ensure consistent and efficient changeover processes.
- Visual Management: Using visual cues to streamline processes and support quick identification of tools and parts during changeovers.
do we think SMED in 1950 could really compare with the super streamlined processes of todays F1 teams?
it could delve deeper into how these practices
nice parallels between F1 pit stops and industrial SMED practices
the challenge lies in scaling this level of precision and teamwork to a continuous production environment, where factors like worker fatigue and tool wear must be meticulously
Related Posts
Best 20 Usages of Proxies For Engineering
How to Sell Ice to Eskimos (aka Marketing Shenanigans)
Greenwashing: A Gentleman’s 15 Best Tips to Exquisite Deception
How-to Best Fight a Pending Patent
All Patent Status: PCT vs Pending Patent vs Published Patent vs Granted Patent
Best 10 Patent Invalidation Strategies and Tools