Single Minute Exchange of Die (SMED) is one of the lean methodologies developed initially by Shigeo Shingo in Japan to increase productivity by decreasing downtimes during change of tools.
For big factory toolings, this is in reality usually still more than one minute although this approach has decreased it by hours if not days.
But in this example, you will even see it opposite … many times per minute! Watch closely and see some common approaches.
– see video below –
Among other SMED technics, you’ll recognize:
Traditionnal SMED technics | … applied here, among others |
Prepare tools in advance |
|
Adapt the tools for the rapid change also, not only for the run (in other parts of this site, this would be similar to “adapt the product to all its life phases”) |
|
Do tasks in parallel | Watch the partner … he is not just holding the screen or performing some miss-direction |
Improve ergonomics | Position preparation (watch the hands position for the last one, the most impressive, just before the “magic”) |
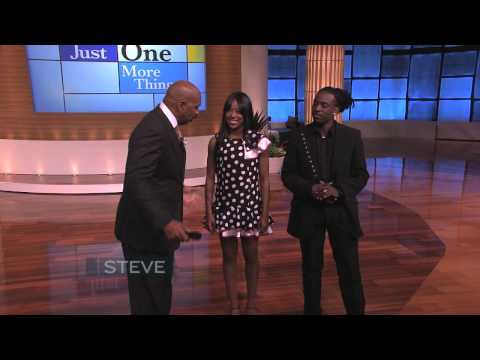
The biggest difference with Industrial application being that in this magic the focus is at the external operations (the changes) while in production, the value added being the internal operations, the rest being wastes.
Interesting take on SMED in magic tricks! But isnt the whole point of magic the mystery, not efficiency?
Interesting read! But arent there some magic tricks where SMED isnt applicable? Not all can be quick change, right?
Related Posts
Best 20 Usages of Proxies For Engineering
How to Sell Ice to Eskimos (aka Marketing Shenanigans)
Greenwashing: A Gentleman’s 15 Best Tips to Exquisite Deception
How-to Best Fight a Pending Patent
All Patent Status: PCT vs Pending Patent vs Published Patent vs Granted Patent
Best 10 Patent Invalidation Strategies and Tools