Or how an already entry-level product can be even cheaper designed and manufactured, with no degradation of end-user experience. Value analysis is the key. What is required for the customer so as for the functions … and stick to that. A full redesign project example, on a very basic, but real product, to show key concepts of the process.
Please add/comment on the right
Disclaimer: innovation.world has no financial incentive whatsoever, nor any ownership in the product reviewed. Products are chosen based on the only factor of having interesting or original designs to share with other industries. These products are on the market for years; Innovation.world has not and does not disclose any special or confidential information, but only what is visible by dismounting, observation and knowledge from similar technologies. Note however that these designs may be patented by their respective owners. |
The chosen product is a stainless-steel cutter

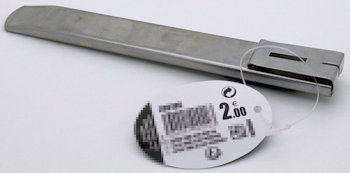
Current Design
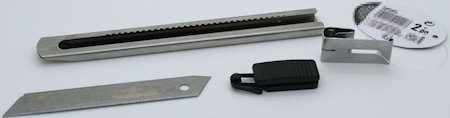
Including shop margin & 20% taxes, the end-user price 2€!
This product is intended to be part of special seasonal offers in big supermarkets, “All for X€ !” manufactured, imported, and sold in big volumes.
As we will see, this product still delivers a lot for such a low price (we have seem more expensive cutters than this one, with more plastic than stainless steel, and the only metal part was thin painted black basic steel.)
Good materials
Overall, quality is very good, stainless steel for the main body as for the clip & of course only one blade sold with the product.
The packaging seems the only trade-off in this design.
btw.: while talking about packaging, having the blade of the cutter unprotected & detachable without breaking any seal is arguable (but likely longer knifes are also sold is such shops, also unprotected)
Possible Redesign
As basic specs, let’s impose some typical constraints on the redesign:
- keep same technologies; no special investments (typical example could have been to overmold metal, to limit stainless steel)
- at least the same quality & robustness (typical example: thinner metal sheet on the main housing or painted low-quality steel)
- use standard cutter blade & provide x1 sample (the biggest constraint as this choice imposes some fixed price, imposes the overall size of the product so as its attachment method)
Current Bill of Materials (BOM)
Detailed to its smallest component:
comments | estimated cost | ||||
Completed assembly | -Main Body | metal sheet, stainless steel, several precise bendings | 60% | ||
-clip sub-assembly | -clip | metal sheet, stainless steel, several bendings with a small radius | 12% | ||
-plastic strip | negligible | ||||
-label | 1% | ||||
-blade sub-assembly | -blade | standard of-the-shelf component | 8% | ||
-knob sub-assembly | -knob body | plastic | 5% | ||
-knob cover | plastic | 4% | |||
-spring | AISI 302? bended | 5% | |||
-Assembly & control | far east? | 5% |
Functional Analyse
-inter-action graph to come-
From the graph, the product has clearly 3 functional groups that cooperate together and needs to be maintained in one way or another.
- the blade: of-the-shelf as per the specs -no change-
- the “blade housing”: guiding the blade + protecting the hand from the rest of the blade while cutting + retracting the blase is a function
- hollowed housing? the back of the body can indeed be hollowed to reduce metal. That would not affect too much its rigidity, gain a bit of weight and “look” more technical. Unfortunately either punched or laser cut, would complexify the process and not much bring the cost down -so a no-go solution-. Note that made of more expensive & recyclable material, the choice would have been different, like copper alloys that have their machine chips very expensive & recyclable)
- shorter housing? the functional length is one of the blades only, as it needs to be retracted fully inside the housing, All the remaining housing length is just due to design choices, if not a waste at least a design inefficiency. This is estimated to be 20% of the housing.
- a “blade stopper”: it can be any mechanism, as long as it permits two functions and with the blade being at various lengths in its lifetime
- take in & out the blade
- hold firmly the blade at different positions
note that although most products on the market solve these 2 functions with 1 sub-assembly, it could be different
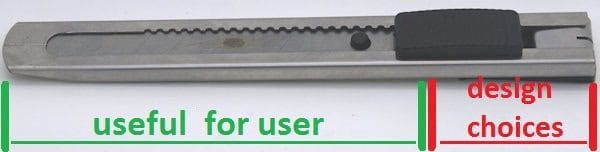
From the functional analysis: the standard blade is the main component, and all is constructed around it. The “cutter” is in fact just a blade holder.
note: a different approach -out of the imposed specs above- could have been to redesign the blade, like including notches on it, or have two cutting sides …
Brainstorming on the BOM components
- main body: main & heaviest part of the product; changing the material to a cheaper would definitively be an option if the cost was the only target. Not an option here
- Label + attachment: not really other cheaper but versatile alternatives. A sticker directly on the product would be cheaper, but would be difficult to rebrand (its basically an OEM product), not very visible at the point-of-sell & difficult for the end user to remove
- assembly: already far east cost, with a relatively small BOM … a small Kaizen event could be possible directly in the assembly line, but for a limited %gain & out of the scope of this project
Innovative solutions not meeting the imposed specs
Coming from the above analysis, innovative solutions, but usable with different specs & context
with the redesign of the blade, by including notches on the blade, the blade stopper(c) can be part of the housing(b) if that one is deformable, likely plastic. If the blade has the notches
-sketch to come-
a peelable housing: a plastic housing around the blade, protecting the hand during usage. It would work as a pencil: to have a fresh tip(blade), the housing would be cut; to obtain the cheapest cutter as possible, that can still hold a standard blade and have it cut to have a fresh
-sketch to come-
Solution #1
-sketch to come-
Solution #2
-sketch to come-
Conclusion
The product was already nicely designed, acceptable quality manufactured & cheap before the project, but still permits some cost reductions even without changing the technologies & quality expected levels
- suppressing the separate end-cap (at least two solutions for that)
- reducing the stainless steel length to its useful part + a minimum length for the button
permits to achieve the -15% Full Factory Cost target
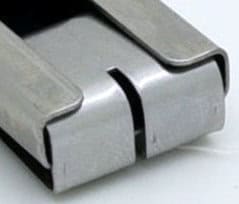
… not to count other ideas seen
Note: one function that has NOT been addressed here is the groove on the end-cap, permitting to cut the blade in pieces once worn -see on the right-
It will be assumed here that users who use cutter so much have other tools & means to do that, like pliers.
Other options in a different context could have been:
- change of technologies (plastics, painted steel …)
- a Lean Sigma approach on the assembly process to reduce its cost (here only for reference, as the assembly is a small part of the cost)
cheapest fully plastic interchangeable but the single-use blade | same technologies, different market positioning low-cost painted metal cutter | different technologies over-molded good grip plastic the blade can firmly be secured in each position |
Interesting article. But isnt a 15% cost reduction too optimistic? It may compromise product quality or functionality, dont you think?
Related Posts
Best 20 Usages of Proxies For Engineering
How to Sell Ice to Eskimos (aka Marketing Shenanigans)
Greenwashing: A Gentleman’s 15 Best Tips to Exquisite Deception
How-to Best Fight a Pending Patent
All Patent Status: PCT vs Pending Patent vs Published Patent vs Granted Patent
Best 10 Patent Invalidation Strategies and Tools