¿Desea aumentar la eficiencia de la producción y del equipo de forma ajustada con SMED? ¿Desea conseguir el tiempo de ciclo más corto (con mucha recursos humanos)? Sigue la organización de los profesionales de F1 del equipo RedBull:
SMED en los equipos de Fórmula 1
[embedyt] https://www.youtube.com/watch?v=8TKE_cA_7z4[/embedyt]
Sólo para tomarles el pelo un poco: las dos herramientas de atornillado tiradas en el suelo al principio ... tal vez un poco de 5S ?
En el vídeo anterior faltaba el repostaje, así que algunos detalles también muy interesantes en la parte del repostaje, con alguna mirada en el conector rápido (¿es eso un gran Stäubli conector de estilo, pero enorme). + mecanismo de bloqueo + la ergonomía del mango de 2 posiciones + seguridad para un caudal de combustible de 12L/segundos.
Aviso también sobre el sistema de comunicación dentro del equipo con el estado en el casco LED indicadores (¿Google glass una década antes?) + operador independiente, tanto por eficacia como por seguridad
[embedyt] https://www.youtube.com/watch?v=OEzouwTVFOo[/embedyt]
Que se compare con el método de los años 50 y luego con otra gran marca, Ferrari en 2013:
[embedyt] https://www.youtube.com/watch?v=RRy_73ivcms[/embedyt]
SMED en 1950
Para tomar sus propias palabras, requiriendo "Sólo 67 segundos después de que el conductor se detuviera"
Apreciamos especialmente al tipo que salta, una y otra vez, para levantar el coche con su peso y su trabajo de martillo para apretar y aflojar una tuerca colocada a mano, claramente, el factor limitante de ese proceso; el utillaje dedicado y el diseño de la conexión del cambio de ruedas (¡condición de uso real cuando se diseña!) es una parte importante del SMED. La regulación de un máximo de 4 miembros de la tripulación que trabajan en la parada en boxes incluye sorprendentemente al conductor -él sólo gira las ruedas-.
SMED de Ferrari en 2013
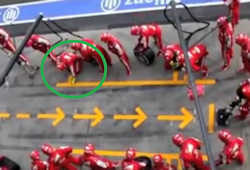
La vista superior permite observar bien un equipo de 3 hombres por rueda (ver en detalle y comparado el trabajo de cuatro equipos, uno por rueda)
Nos gusta especialmente el tercer tipo desde arriba a la izquierda, quitando una especie de pequeña pieza o arenilla en el suelo. A este alto nivel, el fracaso podría venir de cualquier pequeño detalle incontrolado.
Pero sólo para burlarse de este equipo también, si eso fuera una aplicación industrial, calcular la productividad, sabiendo que vemos al menos 21 tipos, con probablemente más fuera de la pantalla ... y comparar con la puntuación de 1950.
Productividad=nb de unidades producidas/persona/unidad de tiempo
A partir de las películas anteriores, en las aplicaciones industriales, el desafío más general podría venir de ser eficiente en la reproducción que en serie, todo el turno de largo, como en la producción de la planta (no tirar la rueda, por ejemplo, que funciona sólo si usted tiene sólo unos pocos para hacer y nada alrededor), pero eso sería una situación diferente.
también asegúrese de su Análisis de Riesgos y FMEA del tipo delante del coche, esperando para levantar el coche, en caso de que el coche no se detenga, o 1m demasiado tarde...
(No hay que confiar en que un humano presione el freno en el milisegundo adecuado, 100% de las veces. En tal caso, en una situación de planta, una parada mecánica construida en el hormigón, moviéndose hacia arriba o hacia abajo podría ser una opción, tal vez levantar el coche también al mismo tiempo).
Lecturas y métodos complementarios
- Metodología 5S: Organización del lugar de trabajo para aumentar la eficiencia y reducir los residuos.
- Producción Justo a Tiempo (JIT): Producir sólo lo que se necesita, cuando se necesita, lo que puede facilitarse mediante cambios rápidos.
- Poka-Yoke (Prevención de errores): Implantación de mecanismos para evitar errores, que pueden ser críticos durante los cambios rápidos.
- Trabajo normalizado: Desarrollo de procedimientos estandarizados para garantizar procesos de cambio coherentes y eficientes.
- Gestión visual: Utilización de señales visuales para agilizar los procesos y facilitar la rápida identificación de herramientas y piezas durante los cambios.
¿creemos que el SMED de 1950 podía compararse realmente con los procesos súper racionalizados de los equipos de F1 actuales?
podría profundizar en cómo estas prácticas
bonitos paralelismos entre las paradas en boxes de la F1 y las prácticas industriales SMED
El reto consiste en trasladar este nivel de precisión y trabajo en equipo a un entorno de producción continua, donde factores como la fatiga de los trabajadores y el desgaste de las herramientas deben ser meticulosamente controlados.
Publicaciones relacionadas
Los 20 mejores usos de los proxies en ingeniería
Cómo Vender Hielo a los Esquimales (o Estrategias de Marketing)
Greenwashing: Los 15 mejores consejos de un caballero para un engaño exquisito
La mejor manera de luchar contra una patente pendiente
Estado de todas las patentes: PCT vs. Patente pendiente vs. Patente publicada vs. Patente concedida
Las 10 mejores estrategias y herramientas para la invalidación de patentes