Did you know thermosetting plastics like epoxy resins are more heat resistant after curing? They are also more chemically stable compared to thermoplastics. This strength and stability make thermosets essential for high-temperature uses in aerospace and automotive fields. But, unlike thermoplastics, thermosets can’t be reshaped or recycled after curing. This key difference makes the discussion on thermoplastics vs thermosets very important.
Key Takeaways
- Thermosets are known for excellent dimensional stability, high strength, and good chemical resistance.
- Thermoplastics can be reshaped and are recyclable, offering high impact resistance and good adhesion to metals.
- Thermosets cannot be recycled and are more heat resistant compared to thermoplastics.
- Common thermoplastics include ABS, PVC, and nylon; common thermosets include epoxy resins and silicone.
Understanding Thermoplastics
Thermoplastics are important polymers used in many industries. They are flexible and adaptable. Unlike thermosets, they can be heated and shaped again many times. This ability means they are efficient to manufacture and easy to recycle.
Characteristics of Thermoplastics
Thermoplastics have several key features. They are tough against impacts and look good. You can join them to metals easily. They can be molded or extruded, giving makers a lot of choices. Polypropylene (PP), polyethylene (PE), and polycarbonate (PC) are among the top types used.
Common Applications of Thermoplastics
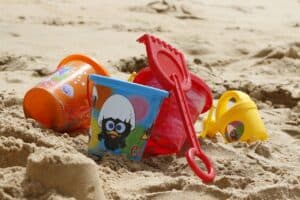
Thermoplastics are used in many things because of their amazing properties, cost and variety of processes.
- Packaging, including food containers and bottles
- Automotive components like dashboards and bumpers
- Textiles and clothing
- Medical devices and supplies
- Consumer electronics and home appliances
- Construction components
- Toys and recreational equipment
This shows how important thermoplastics are in various fields, from healthcare to daily products.
Advantages and Disadvantages of Thermoplastics
It’s key to compare thermoplastics and thermosets. Thermoplastics have many pluses. They can be melted down and reshaped, which is good for the planet. They are usually tougher and cheaper than thermosets. But, they might not do well with UV light and very high heat.
Here’s a look at how thermoplastics and thermosets match up:
Property | Thermoplastics | Thermosets |
---|---|---|
Recyclability | Can be remelted and reused | Cannot be reshaped |
Heat Resistance | Lower | Higher |
Chemical Resistance | Moderate | High |
Toughness | High | Lower |
Cost | Lower | Higher |
Understanding Thermosets
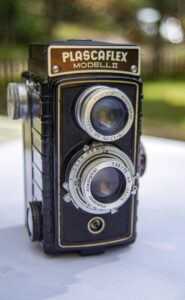
Thermosets are special types of polymers. They bond in a way that can’t be undone once cured. This means they can’t be reshaped or reused after they harden. Thermosets are great at handling high temperatures. This makes them perfect for tough jobs.
Epoxy resins, phenolics, and silicones are common thermosets. They’re used in industries that need strong, durable materials. For instance, aerospace and defense need parts that can handle a lot of stress. The automotive industry uses them for parts exposed to lots of heat and chemicals.
Thermosets have many advantages. They keep their shape well and resist chemicals strongly. That’s why industries like appliance and electrical, energy, and construction use them. They meet the need for reliable materials in these fields.
Here’s a look at some key features of different thermosets:
Thermoset Type | High-Temperature Resistance | Dimensional Stability | Chemical Resistance |
---|---|---|---|
Epoxy Resins | Excellent | Very Good | Very High |
Phenolics | High | Good | High |
Silicones | Exceptional | Excellent | Excellent |
Comparison of Properties
In modern manufacturing, thermoplastics and thermosets play crucial roles. They are key in many industries like electronics, automotive, and construction. A deep properties comparison helps choose the right material for specific needs.
Mechanical Properties
Thermoplastics stand out for their flexibility and impact resistance. They are great for items that face stress and are used often, such as machinery parts or everyday products. Polypropylene (PP) and polyethylene (PE) are common thermoplastics.
Contrarily, thermosets boast more strength and stiffness. They keep their shape under heavy stress, perfect for things like aircraft parts and big machines. Common thermosets include epoxy and phenolic resin.
Thermal Properties
The difference in thermal behavior is clear. Thermoplastics, like polycarbonate (PC) and nylon, can soften or melt when heated. This is handy for recycling because they can be reshaped.
On the flip side, thermosets resist heat better. After curing, they don’t melt and can handle extreme heat. Silicone and polyurethane are key examples, ideal for hot settings.
Chemical Resistance
Chemical resistance also gives important clues. Thermoplastics resist moisture well, making them perfect for food storage and medical tools. They’re also easy to mold, which adds to their versatility.
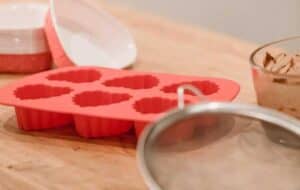
Thermosets, however, fight off corrosive substances better. This property makes them a go-to for chemical gear and in places with lots of harsh chemicals. They’re used in construction adhesives and light watercraft components.
Property | Thermoplastics Characteristics | Thermosets Properties |
---|---|---|
Flexibility | High, excellent impact resistance | Low, high strength and rigidity |
Thermal Resistance | Softens/melts at high temperatures | Withstands high temperatures |
Chemical Resistance | Excellent resistance to moisture | Exceptional resistance to corrosive substances |
Reusability | Recyclable, can be remelted | Non-recyclable, retains shape after curing |
Typical Applications | Food containers, medical devices, textiles | Chemical processing equipment, adhesives, insulation |
Manufacturing Processes for Thermoplastics and Thermosets
Thermoplastics and thermosets are made differently, using their unique traits.
Thermoplastics can be melted and reshaped, thus providing many possibilities:
- Injection Molding: Overmolding, Insert Molding
- Extrusion: Co-extrusion, Blown Film Extrusion
- Thermoforming: Vacuum Forming, Pressure Forming
- Blow Molding: Extrusion Blow Molding, Injection Blow Molding
- Rotational Molding: Biaxial Rotation, Rock and Roll Molding
- 3D Printing: Fused Deposition Modeling (FDM), Selective Laser Sintering (SLS). Note: thermoset materials are progressing in this field
- Compression Molding: Transfer Molding, Bulk Molding Compounds (BMC)
- Calendering: Sheet Calendering, Film Calendering
- Welding: Ultrasonic Welding, Hot Plate Welding
These methods make lots of parts quickly and cheaply. Aluminum molds can be used if volumes are low, which saves money for many industries.
Thermosets need a different approach due to their permanent chemical bonds.
- Reaction injection molding (RIM) is used for thermosets. It allows the material to fill the mold’s details, making strong and complex parts
- resin transfer molding (RTM), also shows how thermosets make detailed and durable components.
- (less frequently, some techniques of thermoplastics can also be used for thermosets)
Molds are often made from aluminum, nickel, or even epoxy, making thermoset tooling comparatively cost-effective, especially for big parts.
Complementary Topics
- Curing Techniques:...
You have read 69% of the article. The rest is for our community. Already a member? Log in
(and also to protect our original content from scraping bots)
Innovation.world community
Login or Register (100% free)
View the rest of this article and all members-only content and tools.
Only real engineers, manufacturers, designers, marketers professionals.
No bot, no hater, no spammer.
FAQ
What are the primary differences between thermoplastics and thermosets?
Thermoplastics and thermosets vary mainly in how they react to heat. Thermoplastics can be heated and cooled many times. This means they can be recycled and reshaped without changing chemically. Thermosets, however, change chemically when heated and can’t be reshaped afterwards. They become strong, durable and temperature-resistant materials.
What are the notable characteristics of thermoplastics?
Thermoplastics are tough and can resist damage well. They look great and stick well to metals. They’re also flexible, making them easy to shape using various methods. For instance, injection molding and extrusion are common. Some familiar examples are polyethylene, polypropylene, and nylon.
What are the advantages and disadvantages of thermoplastics?
Thermoplastics are great because they can be recycled, shaped in many ways, and can take a hit. The downside is they don’t do well under UV light or high heat. This can limit their use in some hot environments.
What are some common types of thermosets?
Epoxy resins, phenolics, and silicones are kinds of thermosets. They handle high heat well, keep their shape, and resist chemicals. This makes them good for tough jobs.
In what applications are thermosets typically used?
Thermosets are perfect for parts that have to handle a lot of stress, insulate electricity, or resist heat. Industries that need materials to stay tough in heat, UV exposure or against chemicals use them a lot.
What are the key differences between the properties of thermoplastics and thermosets?
Generally, thermosets are stronger and more rigid, while thermoplastics are flexible and resist impacts well. Thermosets can handle higher temperatures before getting damaged. They are also better against chemicals. But thermoplastics are better against moisture.
How does the recyclability of thermoplastics compare to thermosets?
Thermoplastics stand out because they can be recycled and reshaped many times. This does not change their chemical makeup. This makes them more sustainable. On the other hand, thermosets can’t be remolded or recycled once they’ve set. This is due to their permanent chemical bonds.
External Links on Thermoplastics and Thermosets
International Standards
(hover the link to see our description of the content)
Usual comparison, but how about considering the environmental impact? How does recycling differ for thermoplastics vs thermosets?
Comments are closed.