Due to their performance yet cheap price, plastic bottles are the highest volume of consumable plastic parts produced, which converts into the highest plastic pollution source on earth. View here the technology principles of plastic bottle manufacturing and the Factory Tours to use them knowingly or find alternatives in your next design.
(2 Factory Tours videos at the bottom of this post)
Plastic Bottles Manufacturing Steps
1. From Petroleum to Pellets
As with most plastic processes, the manufacturing process for plastic bottles begins at a refinery with the creation of plastic pellets that are easy to dose and handle. These pellets are made by combining raw materials (petroleum, natural gas, etc.) with a variety of different chemicals and additives. The exact recipe for the pellets depends on the type of plastic being used, the most common for plastic bottles being PET.
PET = PolyEthylene Terephthalate
More details on Polyethylene Terephthalate are on Wikipedia.
This step is never done at the filling site but in dedicated petroleum transformation factories.
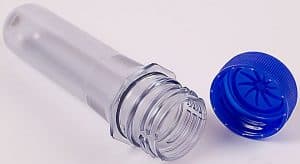
2. From Pellets to Preforms
In blow molding technology, a hollow tube of plastic is first created by traditional plastic injection machines. This so-called “preform” has already the final shape of the screw and the collet, which will be used in the next step for holding the future bottle. The length of the tube will ease the next operation and allow a regular extension of the material.
As no material is later removed, the preform has already the weight of the final empty plastic bottle. Due to the extremely high volume of this market and the little cross-section of this preform, the injection mold has a very high number of cavities, thus producing many preforms per each press cycle. Except for the carrot feeding the mold, very little raw material is wasted.
3. From Preforms to Plastic Bottles
This molding process can be done in a variety of ways, but the most common method is known as “blow molding”. The preform injected in the previous process is then placed over a mold and a blast of hot air is used to blow the tube into the shape of the mold.
Due to the volume of empty plastic bottles, and their clean state at this stage, this step is always done at the final filling factory.
4. Filling And Last Steps
The newly produced bottles are then filled with the final liquid, sealed usually with a plastic screw-on cap, separately injected, usually in PolyEthylene (PE), labeled and marked with:
- product information
- traceability information
- expiration date
and then assembled and packaged into consumer lots and logistic lots, frequently with additional plastic films.
Plastic Bottles Factory Tours
A factory tour of very high volume bottles manufacturing, representative of technologies of the famous brands of juice and sodas manufacturing
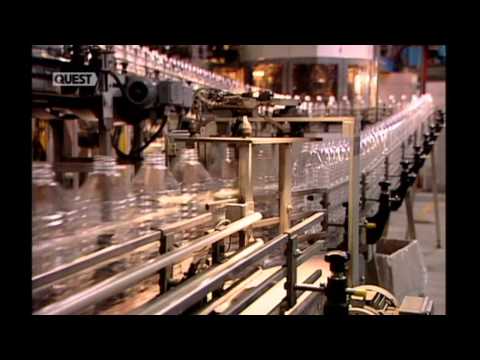
And a much more commercial presentation, but complementary to the previous one
Note: while we agree on the “recyclable” term used in the video, it does not mean effectively recycled in the real life. The degradation of physical properties of recycled compounds, and likely also the costly collection effort required by disseminated trash versus low new material cost, lower the quantity of effectively recycled materials.

Ecological Alternative Approaches
Use fewer consumables
As our Value Analyses moto, follow the first rule:
Do not improve something you can suppress at the first place
- by not buying liquids that can be obtained without bottles at all. Example: tap water in countries with excellent local or national piping distribution systems.
- by using bottles made of reusable glass or reusable plastic. Some countries have a full bottle refilling circuit, usually with a deposit system. The bottles are produced in a similar way as shown above but have much thicker walls to withstand the additional logistic circuit and intense cleaning and disinfection before refilling and relabelling.
- go for the biggest bottle whenever possible. Not only does it contain the biggest quantity of liquid per quantity of plastic material, it also has only one cap compared to several small bottles, but it is way easier to collect as it disseminates less.
Use other Materials
Ask your plastic compounds supplier about bio-sourced plastic alternatives. More and more can be used in traditional injection machines with few parameter changes. Cost is higher but some markets are ready for this. More on these new bio-sourced materials in our ecological design section.
Tip: mind when these raw materials are only used as a percentage, and when the principle is just to split the usual raw plastic material into pieces. Of course, the trash becomes less visible in the field, but in fact, it disseminates the plastics in tiny bits impossible to collect, with almost the same huge degradation time. Instead, look for materials where the core raw material degrades naturally and fast, typically made of starch or equivalent.
Or use no plastic at all, but glass or metals, or other materials. See our dedicated article on this.
Again, only to be used when single-use bottles can not be suppressed completely in the first place.
Complementary Readings & Methods
- Recycling Processes for Plastic Bottles: Explore how plastic bottles are collected, sorted, and reprocessed into new products.
- Innovations in Biodegradable Plastics: Discover advancements in creating eco-friendly alternatives to traditional plastic bottles.
- Regulations and Policies on Plastic Bottles: Understand the global and local regulations governing the use and disposal of plastic bottles.
- Alternative Packaging Solutions: Investigate other materials and designs being used to replace plastic bottles.
- Consumer Behavior and Plastic Usage: Study how consumer habits impact the demand for plastic bottles.
- Energy Consumption in Plastic Production: Assess the energy requirements and efficiency of producing plastic bottles.
- Chemical Composition of Plastics: Learn about the types of plastics used in bottle manufacturing and their chemical properties.
External Links on Plastic Bottles
International Standards
- ISO 8317:2019 Plastic bottles – Child-resistant packaging – Requirements and testing
- ASTM D6400-19:2019 Standard Specification for Labeling of Plastics Designed to be Aerobically Composted in Municipal or Industrial Facilities
- ISO 11607-1:2019 Packaging for terminally sterilized medical devices – Part 1: Requirements for materials, sterile barrier systems and packaging systems
(hover the link to see our description of the content)
Shouldnt we focus more on reducing plastic production rather than understanding its manufacturing process? Just thinking out loud here.
Interesting read! But isnt it ironic that we use petroleum, a non-renewable resource, to produce something so disposable as plastic bottles?
Related Posts
Best 10 Patent Invalidation Strategies and Tools
Life Cycle Assessment (LCA) In Product Design Specifically
Product Value Analysis Overview
Workstation Ergonomic Assessment
Engineering Change Order (ECO): Best Practices to Minimize Disruption and Cost
From Lab To Market: The Role of the Pilot Production Run