When lightweight is not just a cost optimization but the main criteria of the product to function. Can you make a military tank fly? Or how to enter the virtuous cycle of making a light frame permits to put smaller motor, that permits to put smaller batteries, that permits (…).
Also a great example of using existing off-the-shelf cross-components to achieve very low consumer costs.
{snippet review|Hubsan|http://www.hubsan.com}
When it comes to a flying toy, every gram counts. And when the target is even to make that as cheap as possible, designers need to make smart use of off-the-shelf components.
Design
Already, the box is thought lean: 2 simple elastic bands to hold the product safely but easy to put or detach.
The main copter’s body
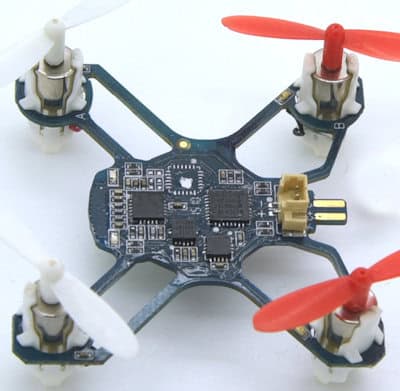
A very nice piece of product design.
The main frame is achieved at the same time:
- the physical structure of the copter without any other assembly required. The CNC cut permits an advanced shape so as hollowing the 4 arms, reducing, even more, the weight
- the frame is the PCB itself! which permits all electronics components to be directly soldered on it, avoiding fixing a separate PCB; It permits also to route the two poles of the 4 motors directly on the 4 frame arms without the need for additional wires (except the ones directly on the motor -read the suggestion on that below-)
- one protrusion of the PCB it at the same time the power connector. To ensure a right +/- polarity connection, the poka-yoke is just a CMS resistor mounted on one side, thus avoiding user mistakes. This resistor is mounted as the other electronic components on the board.
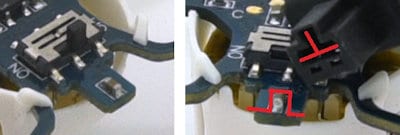
The other genius idea is the choice of a standard micro-size motor used in the phone industry.
Specially made, these ones would cost a fortune, but as they are used as vibrator actuators in very high volumes, these of-the-shelve motors are not only very reliable but very low cost also.
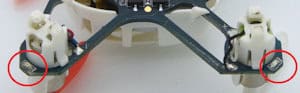
4 LEDs, 2 red & 2 blue, are placed at the extremities of the arm to help the pilot to distinguish the front from the back of the drone during flight, as the drone has an overall round shape. These LEDs are simply routed in parallel to the motor, thus avoiding additionally dedicated PCB routing.
The battery is just maintained in place with double face tape to the PCB and later surrounded by the main body cover.
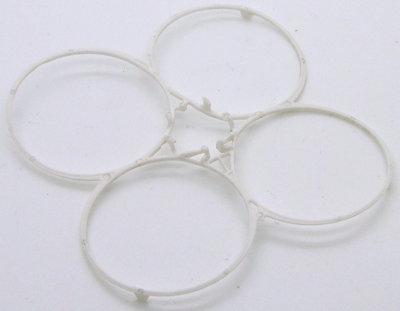
Blade protection Frame
Made light and flexible, the frame is intended to protect the user’s fingers from the blades, and the blades from any shock against surroundings during the pilot learning phase.
This is the thinnest injected part of this product; 6 ejectors per circle are required to take the part out of the mold.
Motor cage
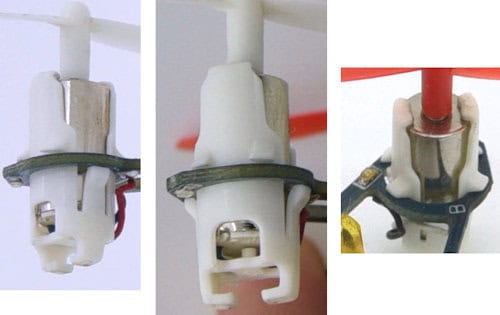
A piece of art in terms of design to achieve a 2 parts mold only (just follow the parting line!)
Cut-offs permit, within 15mm:
- the cage around the motor + 2 clips on the top, maintaining the motor after inserting
- 4 end-stops around the PCB + 2 clips
- a bottom pin, providing the motor both for venting passages and clearance for wires
- 2 “foots” on the bottom, acting as a landing supports (really necessary? Hypothesis: these were possibly to allow a different passage for the wires)
Main Body Cover
Very fine plastic injection, with hollowing design that achieves 4 goals:
- nice visual design, with technical shapes
- holding the battery & protecting the components both from the user’s fingers and from potential shock during (end of) flight
- space for venting the electronics components, including the battery
- permitting a 1-movement mold design
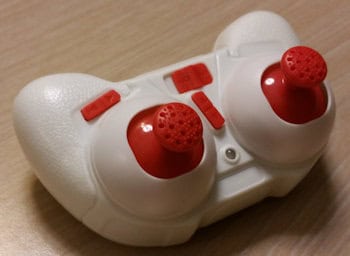
Remote control
Obviously less design & optimization effort on this one. Just does its jobs for such price level.
Purely functional and not intended to withstand chocs.
Its size is really the minimum to be held correctly by two adult hands.
The body is made out of 3 basic parts, including the battery cover. Functions include the 2 typical joysticks to be controlled by thumbs.
Conclusion
Thumbs up! A great demonstration of smart components choice, value analyses to restrict everything to its minimum, and plastic design. Not counting a nice injection work for such thin deformable parts & frames.
Likely the design process has started with the available micro motor (see article on that) and the rest then being adapted around, ie overall frame size and then the choice of battery
All that permitting, to our knowledge, the smallest mass-produced drone toy, but still maintaining a cheap really affordable product.
Possible Improvements?
Compatible in that price range & toy market segment, we see only very minor ones:
- slightly shaping the PCB frame legs more even and directly to the body; an even further improvement could be to link the 4 arms by a circular path, making the drone more rigid, at the cost of not-so-good PCB placement optimization on the total sheet & associated PCB material losses
- some plastic indexing shape in the motor cage, and its female counter shape in the PCB, to avoid the motor cage to turn
- a possible production improvement: if the motors would sit on the PCB rather than being in the median plane, it means a complete redesign of the cage, and the motor’s two pins could be connected directly on the PCB with through-holes soldering, avoiding the 8 wires completely and associated 2x2x4 manual soldering. Rigidity and overall quadcopter typical design to be confirmed
Possible innovations?
As the price of small components decreases, next generation could include some height + sides distance sensors to allow easier control of height and obstacle avoidance for beginner pilots or fast races?
Some research labs have already demonstrated some incredible co-op between flying drones. Combined with the sensor suggestion above this drone could become a nice DIY drone platform and gain an additional massive customer base by being programmable? (some open-source USB-programmable chip + a slightly bigger USB connector).
Does anyone else think the blade protection frame might compromise the quadcopters balance? Just throwing it out there!
Interesting read, but isnt a simpler motor cage design better for maintenance? Blade protection might affect aerodynamics, right?
The use of off-the-shelf components like phone vibrator motors is a brilliant example of leveraging existing technology to reduce costs and enhance reliability
it would be interesting to explore how these principles might be adapted for larger-scale applications, such as in military or commercial drones
It’s impressive how the integration of the PCB as both the frame and circuit board reduces unnecessary components, but I wonder if this approach might limit the ability to make repairs or upgrades in the future
Related Posts
How to Sell Ice to Eskimos (aka Marketing Shenanigans)
Greenwashing: A Gentleman’s 15 Best Tips to Exquisite Deception
How-to Best Fight a Pending Patent
All Patent Status: PCT vs Pending Patent vs Published Patent vs Granted Patent
Best 10 Patent Invalidation Strategies and Tools
Life Cycle Assessment (LCA) In Product Design Specifically