Small tips are useful when considering small electrical motors when designing a new product.
- for the same power, the best efficiency of the motor is obtained at high velocities
- Low speed & high torque is obtained via a higher magnetic field, thus requiring a higher load & more wiring
- On the first factor, the price of the motor is proportional to the quantity of copper wiring inside
So from the above:
If your design and users can stand the higher noise due to higher speed rotation and potentially higher friction and heat, always take the higher speed choice you can afford. It will decrease costs, weight & size.
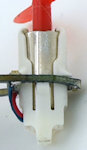
Tip: thanks to the phone industry, the industry has access now to a very high volume produced of micro size motors, initially intended for vibration function of mobile cells.
This vibration is obtained by a small out-off-axis load. Do consider using these motors in your small product designs; not to say that these motors cost pennies only when supplied in the far east.
Typical size: dia.=4mm & lengh 10mm but smaller version with lengh <5mm exists
A great design example using such motors
See the directory for online tools for motor dimensioning, the trade-off always being to use a gearbox and the smallest motor possible, or a bigger motor actuating directly and reducing complexity. From the Tip above, in some cases, the recent solution is to put several motors (ie one per function, like one per wheel)
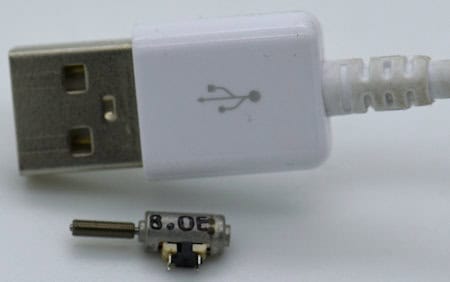
Interesting read! But has anyone considered how these design factors could impact the recycling process of electric motors?
Interesting read, but did they consider the effect of magnetic field strength on small electric motor efficiency? Just curious.
Interesting article! But wouldnt the efficiency of electric motors be more related to how theyre used than their design?
Design dictates function. Even the best usage cant fix poor engineering.
Interesting article, but isnt it true that the efficiency of electric motors can significantly drop at low speeds?
Has anyone considered how these electric motor designs would fare in extreme weather conditions?
Related Posts
Best 20 Usages of Proxies For Engineering
How to Sell Ice to Eskimos (aka Marketing Shenanigans)
Greenwashing: A Gentleman’s 15 Best Tips to Exquisite Deception
How-to Best Fight a Pending Patent
All Patent Status: PCT vs Pending Patent vs Published Patent vs Granted Patent
Best 10 Patent Invalidation Strategies and Tools