Did you know poka-yoke can greatly reduce defect rates and improve product quality? It does more than just lower mistakes. Poka-yoke boosts productivity, lifts worker morale, and saves money on scrap and inspections. In today’s competitive manufacturing world, minor errors can have big effects. This Japanese method leads to better efficiency and quality control.
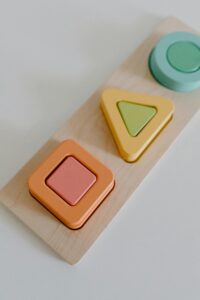
Poka-yoke means “fool-proofing” in Japanese. It’s a key part of lean manufacturing.
It uses four key principles: elimination, prevention, detection, and mitigation. These principles help make sure everything works right the first time. This method is great for stopping errors and controlling quality. It reduces mistakes made by both people and machines.
L'introduzione di poka-yoke nella produzione e nei servizi aiuta a individuare gli errori rapidamente o addirittura prima che si verifichino. In questo modo si evitano i danni prima che possano influire sul prodotto finale. Il metodo mantiene alta la qualità senza aumentare i costi. Combina le competenze umane con strategie a prova di errore. In questo modo, le aziende possono realizzare prodotti di alta qualità mantenendo una forza lavoro qualificata.
Punti chiave
- Poka-yoke, or “fool-proofing,” is key to making fewer mistakes and better quality control.
- L'utilizzo di questo sistema porta a una riduzione dei difetti e a prodotti finali migliori.
- Un buon metodo di poka-yoke migliora la produttività e il morale del lavoro, riducendo i costi.
- Si concentra sui principi di eliminazione, prevenzione, rilevamento e mitigazione.
- Miscelazione ergonomico Il design con il poka-yoke può ridurre la stanchezza e l'affaticamento mentale dei lavoratori.
- A partire dal Sistema di produzione ToyotaIl poka-yoke è fondamentale nelle aree di produzione e di servizio.
- Il Poka-yoke utilizza tecniche come il contatto, il valore fisso e il movimento-passo per processi privi di errori.
Capire le origini e i principi del Poka-Yoke
Poka-yoke started in the 1960s by Shigeo Shingo, part of Toyota’s approach. It aimed for zero defects in manufacturing. Its goal is to stop mistakes or make them clear right away.
L'origine del Poka-Yoke
Shingo voleva migliorare l'accuratezza della produzione. È passato da "a prova di idiota" a "a prova di errore" per evitare la negatività. Il primo strumento assicurava che le catene di montaggio non mancassero le molle, dimostrando che le idee semplici possono prevenire gli errori.
Principi chiave del Poka-Yoke
Il Poka-yoke si concentra sull'arresto, l'evidenziazione e la correzione rapida dei difetti. Rende la produzione migliore e più affidabile. Esistono metodi di controllo per bloccare gli errori e metodi di avviso per segnalare possibili errori.
Tipi di tecniche di Poka-Yoke
Poka-yoke techniques are grouped into three types aimed at stopping errors. They help to automatically spot what’s not right. These methods are used in many areas, like healthcare and cars, to get better quality and efficiency.
Metodo di contatto
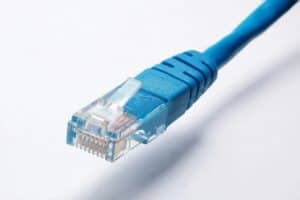
Il metodo di contatto utilizza elementi come le dimensioni, la forma, il colore o il peso per trovare gli errori. Controlla se ci sono le caratteristiche giuste prima di andare avanti. Questo aiuta a garantire che le cose siano corrette fin dall'inizio.
I sensori che controllano le dimensioni e la codifica a barre per i farmaci corretti ne sono un esempio. Inoltre, i pedali della frizione nelle automobili prevengono gli incidenti. Questo metodo riduce la necessità di rifare il lavoro e rende le operazioni più affidabili.
Metodo a valore fisso
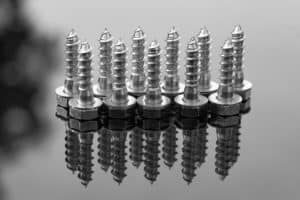
The fixed-value method makes sure the right amount of actions or parts are completed. It’s used a lot on assembly lines for exact repetition. This keeps quality high and errors low.
Un sensore potrebbe contare le viti per assicurarsi che non ne manchi nessuna. Tiene traccia di ogni passaggio per mantenere alta la qualità. Questo sistema è spesso utilizzato nell'elettronica per assicurarsi che tutte le parti siano inserite correttamente.
Metodo Motion-Step
Il metodo motion-step controlla che ogni fase venga eseguita nell'ordine giusto. Elimina gli errori dovuti all'esecuzione di attività fuori sequenza. In questo modo si garantisce che tutto venga eseguito correttamente.
Nella produzione di oggetti, l'assemblaggio dei pezzi in ordine è fondamentale. In questo modo ci si assicura che ogni azione sia corretta prima della fase successiva. Questo metodo rende i processi più fluidi e aumenta l'efficienza della produzione.
Esempio: un coperchio non può essere assemblato se manca un componente interno (tra l'altro: lo stesso principio utilizzato in molti aspirapolvere di largo consumo: il coperchio non può essere chiuso se manca il sacchetto)
Using these poka-yoke techniques in making things focuses on stopping mistakes. It also makes things safer, cuts costs and makes customers happy by consistently giving them good products.
Vantaggi dell'implementazione del Poka-Yoke nel vostro processo produttivo
L'utilizzo del poka-yoke nella produzione offre molti vantaggi. Migliora la qualità e riduce i costi legati ai difetti e alle rilavorazioni. Questo aiuta enormemente le aziende.
Questo approccio promuove il miglioramento continuo e riduce la necessità di molti controlli e formazione grazie ai suoi autocontrolli.
One key advantage of poka-yoke is cost reduction. It significantly reduces waste, scraps, and rework costs. By minimizing downtime, it also increases the efficiency of manufacturing. Using poka-yoke tools like contact methods, fixed-value methods, and motion-step methods helps spot and fix errors fast. This stops defects from leading to bigger problems.
Poka-yoke also makes the workplace safer. It catches errors early to prevent accidents, making a safer place for workers. This boosts their morale and job satisfaction, which in turn increases productive output.
Beneficio | Descrizione |
---|---|
Miglioramento della qualità | Improved product quality through error prevention and detection. |
Riduzione dei costi | Riduzione delle spese grazie alla riduzione degli scarti, degli sfridi e delle rilavorazioni. |
Efficienza produttiva | Aumento della produttività grazie alla riduzione dei tempi di inattività e degli errori. |
Sicurezza sul lavoro | Maggiore sicurezza grazie alla prevenzione di errori umani che potrebbero causare incidenti. |
Morale dei dipendenti | Aumento della soddisfazione e dell'impegno sul lavoro grazie alla semplificazione dei processi. |
Soddisfazione del cliente | Una qualità costante dei prodotti porta a una maggiore fiducia e fedeltà dei clienti. |
Come integrare efficacemente il Poka-Yoke nel vostro controllo qualità
L'integrazione del poka-yoke nel controllo qualità è fondamentale per individuare tempestivamente i difetti e migliorare la qualità della produzione. Si tratta di fasi che creano un solido sistema di controllo della qualità.
Progettazione di processi per segnali di errore
Dopo aver individuato i punti in cui potrebbero verificarsi degli errori, progettate dei processi che vi avvisino di tali errori. Ciò può avvenire attraverso avvisi o arresti quando qualcosa non è in regola. In questo modo si evita che il lavoro difettoso continui.
- Utilizzate soluzioni tecnologiche come i sistemi pick-to-light, i fasci di luce e i controlli visivi.
- Aggiungere funzioni di arresto che si attivano quando vengono individuati degli errori.
Ruolo del coinvolgimento dei dipendenti
È molto importante che i dipendenti siano coinvolti nel poka-yoke e nel controllo qualità. Conoscono bene il flusso di lavoro e vedono i problemi più comuni. Il loro aiuto nell'individuare e correggere i difetti può portare a un miglioramento continuo e a una migliore qualità.
"I nostri lavoratori in prima linea sono spesso la più grande fonte di innovazione nel rilevamento e nella prevenzione degli errori", ha osservato una Toyota Esperto di sistemi di produzione.
Ergonomia e Poka-Yoke: Creare un luogo di lavoro più sicuro
Miscelazione ergonomia con poka-yoke rende i luoghi di lavoro più sicuri ed efficienti. Poka-yoke ergonomico significa progettare strumenti e spazi per ridurre lo sforzo. Inoltre, aiuta a prevenire gli errori dovuti a stanchezza o svista. Questo approccio consente ai lavoratori di svolgere il proprio lavoro in modo confortevole, riducendo i rischi di infortunio e mantenendo alta la produttività.
When we add ergonomic error-proofing to production, we focus on safety and avoiding mistakes. Using ergonomic designs, like adjustable stations and natural movement tools, works well with poka-yoke. Add in visual aids and physical barriers, and the workplace gets even safer for everyone.
I risultati di questa strategia combinata sono enormi. Migliora le condizioni di lavoro, riducendo gli infortuni e gli errori. Questo non si limita a mantenere i dipendenti al sicuro, ma crea una cultura dell'eccellenza.
Letture correlate
- Industrial engineering: focuses on the optimization of complex processes or systems, integrating people, materials, information, equipment, and energy to improve production efficiency.
- Error proofing: techniques and strategies designed to prevent mistakes in manufacturing and service processes.
Standard work: establishing and documenting the best practices for performing work consistently and efficiently.
Link esterni sulla produzione a prova di errore e di qualità
Standard internazionali
(passa il mouse sul link per vedere la nostra descrizione del contenuto)