Did you know poka-yoke can greatly reduce defect rates and improve product quality? It does more than just lower mistakes. Poka-yoke boosts productivity, lifts worker morale, and saves money on scrap and inspections. In today’s competitive manufacturing world, minor errors can have big effects. This Japanese method leads to better efficiency and quality control.
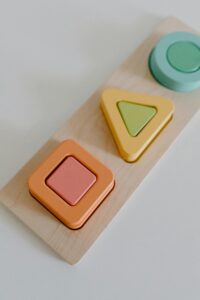
Poka-yoke means “fool-proofing” in Japanese. It’s a key part of lean manufacturing.
It uses four key principles: elimination, prevention, detection, and mitigation. These principles help make sure everything works right the first time. This method is great for stopping errors and controlling quality. It reduces mistakes made by both people and machines.
L'utilisation du poka-yoke dans la fabrication et les services permet de détecter les erreurs rapidement, voire avant qu'elles ne se produisent. Cela permet d'arrêter les dommages avant qu'ils n'affectent le produit final. Cette méthode permet de maintenir un niveau de qualité élevé sans augmenter les coûts. Elle associe les compétences humaines à des stratégies à l'épreuve des erreurs. Les entreprises peuvent ainsi fabriquer des produits de qualité supérieure tout en conservant une main-d'œuvre qualifiée.
A Retenir
- Poka-yoke, or “fool-proofing,” is key to making fewer mistakes and better quality control.
- Son utilisation permet de réduire les défauts et d'améliorer les produits finaux.
- Les bonnes méthodes de poka-yoke améliorent la productivité et le moral des travailleurs tout en réduisant les coûts.
- Il se concentre sur les principes d'élimination, de prévention, de détection et d'atténuation.
- Mélange ergonomique Le design avec le poka-yoke peut réduire la fatigue des travailleurs et la charge mentale.
- À partir de la Système de production ToyotaLe poka-yoke est essentiel dans les secteurs de l'industrie et des services.
- Le Poka-yoke utilise des techniques telles que le contact, la valeur fixe et l'étape du mouvement pour des processus sans erreur.
Comprendre les origines et les principes du Poka-Yoke
Poka-yoke started in the 1960s by Shigeo Shingo, part of Toyota’s approach. It aimed for zero defects in manufacturing. Its goal is to stop mistakes or make them clear right away.
L'origine du Poka-Yoke
Shingo voulait améliorer la précision de la production. Il est passé de "idiot-proofing" à "error-proofing" pour éviter toute négativité. Le premier outil a permis de s'assurer que les chaînes de montage ne manquaient pas de ressorts, montrant ainsi que des idées simples peuvent prévenir les erreurs.
Principes clés du Poka-Yoke
Le Poka-yoke se concentre sur l'arrêt, la mise en évidence et la correction rapide des défauts. Il permet d'améliorer la fabrication et de la rendre plus fiable. Il existe des méthodes de contrôle pour bloquer les erreurs et des méthodes d'alerte pour signaler les erreurs possibles.
Types de techniques Poka-Yoke
Poka-yoke techniques are grouped into three types aimed at stopping errors. They help to automatically spot what’s not right. These methods are used in many areas, like healthcare and cars, to get better quality and efficiency.
Méthode de contact
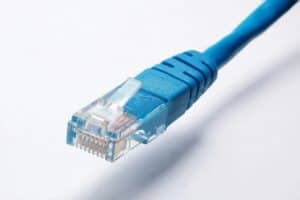
Le méthode de contact utilise des éléments tels que la taille, la forme, la couleur ou le poids pour détecter les erreurs. Il vérifie si les bonnes caractéristiques sont présentes avant de poursuivre. Cela permet de s'assurer que les choses sont correctes dès le départ.
Les capteurs qui vérifient les dimensions et les codes-barres pour les médicaments sont des exemples. De même, les pédales d'embrayage des voitures préviennent les accidents. Cette méthode permet de réduire le nombre de travaux à refaire et de rendre les opérations plus fiables.
Méthode de la valeur fixe
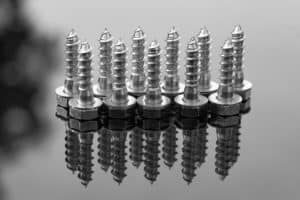
The fixed-value method makes sure the right amount of actions or parts are completed. It’s used a lot on assembly lines for exact repetition. This keeps quality high and errors low.
Un capteur peut compter les vis pour s'assurer qu'il n'en manque aucune. Il suit chaque étape pour maintenir la qualité. Cette technique est souvent utilisée en électronique pour s'assurer que toutes les pièces sont correctement installées.
Méthode par étapes
Le méthode par étapes vérifie que chaque étape est effectuée dans le bon ordre. Il corrige les erreurs commises lors de l'exécution des tâches dans le désordre. Cela permet de s'assurer que tout est fait correctement.
Dans la fabrication d'objets, il est essentiel d'assembler les pièces dans l'ordre. Il permet de s'assurer que chaque action est correcte avant l'étape suivante. Cette méthode rend les processus plus fluides et augmente l'efficacité de la production.
Exemple : un couvercle ne peut pas être assemblé s'il manque un composant interne (btw : même principe utilisé dans de nombreux aspirateurs grand public : le couvercle ne peut pas être fermé s'il manque le sac)
Using these poka-yoke techniques in making things focuses on stopping mistakes. It also makes things safer, cuts costs and makes customers happy by consistently giving them good products.
Avantages de l'intégration du Poka-Yoke dans votre processus de fabrication
L'utilisation du poka-yoke dans la fabrication offre de nombreux avantages. Il améliore la qualité et réduit les coûts liés aux défauts et aux reprises. Cela aide énormément les entreprises.
Cette approche favorise l'amélioration continue et réduit la nécessité de nombreux contrôles et formations grâce aux autocontrôles.
One key advantage of poka-yoke is cost reduction. It significantly reduces waste, scraps, and rework costs. By minimizing downtime, it also increases the efficiency of manufacturing. Using poka-yoke tools like contact methods, fixed-value methods, and motion-step methods helps spot and fix errors fast. This stops defects from leading to bigger problems.
Poka-yoke also makes the workplace safer. It catches errors early to prevent accidents, making a safer place for workers. This boosts their morale and job satisfaction, which in turn increases productive output.
Avantage | Description |
---|---|
Amélioration de la qualité | Improved product quality through error prevention and detection. |
Réduction des coûts | Diminution des dépenses grâce à la réduction des déchets, des rebuts et des reprises. |
Efficacité de la fabrication | Augmentation de la productivité en minimisant les temps d'arrêt et les erreurs. |
Sécurité sur le lieu de travail | Amélioration de la sécurité par la prévention des erreurs humaines susceptibles d'entraîner des accidents. |
Moral des employés | Amélioration de la satisfaction au travail et de l'engagement grâce à la rationalisation des processus. |
Satisfaction des clients | Une qualité constante des produits permet d'accroître la confiance et la fidélité des clients. |
Comment intégrer efficacement le Poka-Yoke dans votre contrôle de la qualité ?
L'intégration du poka-yoke dans le contrôle de la qualité est essentielle pour détecter rapidement les défauts et améliorer la qualité de la production. Il s'agit d'étapes qui permettent de mettre en place un système de contrôle de la qualité solide.
Conception de processus pour les signaux d'erreur
Après avoir déterminé où des erreurs peuvent se produire, concevez des processus qui vous avertissent de ces erreurs. Il peut s'agir d'avertissements ou d'arrêts lorsque quelque chose n'est pas sur la bonne voie. Cela permet d'empêcher la poursuite d'un travail défectueux.
- Utiliser des solutions techniques telles que les systèmes "pick-to-light", les faisceaux de freinage et les contrôles de la vision.
- Ajouter des fonctions d'arrêt qui se déclenchent lorsque des erreurs sont détectées.
Rôle de la participation des employés
Il est très important que les employés participent au poka-yoke et au contrôle de la qualité. Ils connaissent bien le flux de travail et sont conscients des problèmes courants. Leur aide pour repérer et corriger les défauts peut conduire à une amélioration continue et à une meilleure qualité.
"Nos travailleurs de première ligne sont souvent la plus grande source d'innovation en matière de détection et de prévention des erreurs. Toyota Expert en systèmes de production.
Ergonomie et Poka-Yoke : Créer un lieu de travail plus sûr
Mélange ergonomie avec poka-yoke rend les lieux de travail plus sûrs et plus efficaces. L'ergonomie poka-yoke consiste à concevoir des outils et des espaces qui réduisent les contraintes. Il permet également d'éviter les erreurs dues à la fatigue ou à la négligence. Cette approche permet aux travailleurs de faire leur travail confortablement, ce qui réduit les risques de blessures et maintient la productivité.
When we add ergonomic error-proofing to production, we focus on safety and avoiding mistakes. Using ergonomic designs, like adjustable stations and natural movement tools, works well with poka-yoke. Add in visual aids and physical barriers, and the workplace gets even safer for everyone.
Les résultats de cette stratégie combinée sont énormes. Elle améliore les conditions de travail, ce qui réduit le nombre de blessures et d'erreurs. Cela ne permet pas seulement d'assurer la sécurité des employés, mais aussi d'instaurer une culture de l'excellence.
Lectures connexes
- Industrial engineering: focuses on the optimization of complex processes or systems, integrating people, materials, information, equipment, and energy to improve production efficiency.
- Error proofing: techniques and strategies designed to prevent mistakes in manufacturing and service processes.
Standard work: establishing and documenting the best practices for performing work consistently and efficiently.
Liens externes sur la fabrication de qualité et à l'abri des erreurs
Normes internationales
(survolez le lien pour voir notre description du contenu)