Vous voulez augmenter l'efficacité de la production et de l'équipe de façon rationnelle avec la SMED ? Vous voulez atteindre le temps de cycle le plus court (avec beaucoup de ressources humaines) ? Suivez l'organisation des pros de la F1 de l'équipe RedBull :
SMED dans les équipes de Formule 1
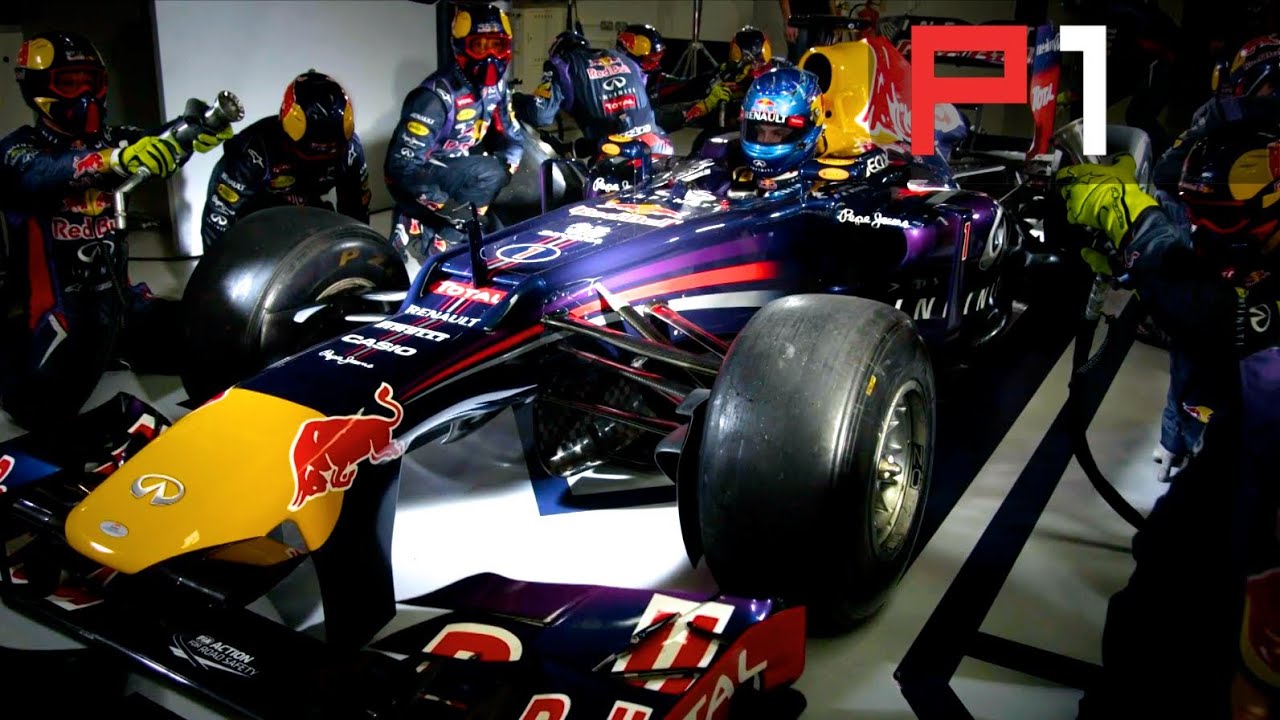
Just to tease them a bit: the two screwing tools lying on the floor at the beginning … maybe a bit of 5S ?
Le ravitaillement en carburant était absent de la vidéo ci-dessus, donc quelques détails aussi très intéressants sur la partie ravitaillement, avec un regard sur le connecteur rapide (est-ce un gros... Stäubli style connector, but huge?) + locking mechanism + the ergonomic of the 2 positions handle + security for 12L/seconds fuel flow.
Notice also on the communication system within the team with in-helmet status LED indicators (Google glass a decade before ?) + independent operator, for efficiency so as for security

A comparer avec la méthode des années 50, puis avec une autre grande marque, Ferrari en 2013 :

SMED en 1950
Pour reprendre ses propres mots, il faut "Juste 67 secondes après que le conducteur se soit arrêté"
Nous avons particulièrement apprécié le gars qui sautait, encore et encore, pour soulever la voiture avec son poids et le travail du marteau pour serrer et desserrer un écrou placé à la main, clairement, le facteur limitant de ce processus ; l'outillage dédié et la conception de la connexion de changement de roue (condition d'utilisation réelle lors de la conception !) est une partie importante du SMED. La réglementation concernant le maximum de 4 membres d'équipage travaillant sur l'arrêt au stand inclut étonnamment le conducteur - il ne fait que tourner les roues -.
SMED par Ferrari en 2013
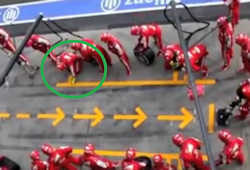
La vue de dessus permet de bien observer une équipe de 3 hommes par roue (regarder en détail et comparer le travail de quatre équipes, une par roue).
Nous aimons particulièrement le 3ème type en haut à gauche, qui enlève une sorte de petite pièce ou de gravillon sur le sol. À ce niveau, l'échec peut provenir de n'importe quel petit détail non maîtrisé.
Mais juste pour taquiner cette équipe aussi, si c'était une application industrielle, calculer la productivitésachant que nous voyons au moins 21 gars, avec probablement plus hors de l'écran ... et comparer au score de 1950.
Productivité=nb d'unités produites/personne/unité de temps
D'après les films ci-dessus, dans les applications industrielles, le défi plus général pourrait venir de l'efficacité à reproduire cela en série, pendant toute la durée de l'équipe, comme dans la production d'une usine (ne pas jeter la roue par exemple, cela ne fonctionne que si vous n'avez que quelques-unes à faire et rien autour), mais ce serait une situation différente.
soyez également sûr de votre analyse de risque et de l'AMDEC du gars devant la voiture, attendant de soulever la voiture, au cas où la voiture ne s'arrêterait pas, ou 1m trop tard...
(Ne comptez pas sur un humain qui appuie sur le frein à la bonne milliseconde, 100% du temps. Dans ce cas, dans une situation d'usine, un arrêt mécanique construit dans le béton, se déplaçant vers le haut ou le bas pourrait être une option, peut-être en soulevant la voiture aussi en même temps).
Lectures et méthodes complémentaires
- 5S Methodology: Organizing the workplace to increase efficiency and reduce waste.
- Just-In-Time (JIT) Production: Producing only what is needed, when it is needed, which can be facilitated by quick changeovers.
- Poka-Yoke (Error Proofing): Implementing mechanisms to prevent errors, which can be critical during rapid changeovers.
- Standard Work: Developing standardized procedures to ensure consistent and efficient changeover processes.
- Visual Management: Using visual cues to streamline processes and support quick identification of tools and parts during changeovers.
Quelle est l'utilité de ce message ?
Cliquez sur une étoile pour l'évaluer !
Note moyenne 5 / 5. Décompte des voix : 2
Aucun vote pour l'instant ! Soyez le premier à évaluer cet article.
Nous sommes désolés que cet article ne vous ait pas été utile !
Améliorons cet article !
Comment pouvons-nous améliorer cet article ?
it could delve deeper into how these practices
nice parallels between F1 pit stops and industrial SMED practices
the challenge lies in scaling this level of precision and teamwork to a continuous production environment, where factors like worker fatigue and tool wear must be meticulously